GRUPOS TECNOLOGICOS
1. Definición y conceptos.
La tecnología de grupos es un enfoque para manufactura en el cual se identifican y agrupan partes similares para aprovechar sussimilitudes en el diseño y la producción.
La tecnología de grupos es un enfoque para la producción de partes en cantidades medias. Las partes (y los productos) en este rango decantidad por lo general se hacen en lotes, y la producción en lotes tiene las siguientes desventajas:
1. Tiempo de detención para cambios
2. Costos altos de realización de inventarios.La tecnología de grupos GT (Group Technology) minimiza estas desventajas reconociendo que, aunque las partes son distintas, poseen similitudes. La TG explota las similitudes delas partes utilizando procesos y habilitación de herramientas similares para producirlas.
Las similitudes entre las partes permite clasificarlas en familias. No es extraño que unafábrica que produce 10000 partes diferentes sea capaz de agrupar la mayoría de ellas en 20 ó 30 familias de partes. En cada familia de partes, los pasos de procesamiento son similares. Cuandoestas similitudes se aprovechan en la producción, mejora la eficiencia operativa. En general el mejoramiento se obtiene organizando las instalaciones de producción en celdas demanufactura. Cada celda se diseña para producir una familia de partes (o una cantidad limitada de familias de partes), con lo que sigue el principio de la especialización de las operaciones.Clasificación y codificación de partes.
Una familia de partes es un grupo de partes que poseen similitudes en la forma geométrica y el tamaño, o en los pasos de procesamientoque se usan en su manufactura. siempre hay diferencias entre las partes en una familia, pero las similitudes son lo bastante cercanas para poder agrupar las partes en la misma familia
- Distribución por células o híbridas

- Célula de un trabajador, múltiples máquinas:
Esta distribución reduce los niveles de inventario ya que los materiales pasan directamente a la siguiente operación, en lugar de apilarse en pilas de espera.

- Tecnología de grupo:
ANTES:


Acción - implantación
- 6. Implantación de la alternativa elegida
ÁREAS DE LA EMPRESA

FLUJOGRAMA DEL PROCESO PRODUCTIVO

9 s de la calidad
La cultura, constituida por tradiciones o costumbres propias, heredadas a través del
tiempo y transmitidas entre todos los pobladores de cada país del mundo, sin importar su
latitud, tiene incidencia directa sobre el comportamiento del consumidor. El ámbito cultural
del consumidor, a su vez, incluye subcategorías, entendidas como sectores identificables
dentro de una sociedad más grande y compleja. Los miembros de esas subculturas poseen
creencias, valores y costumbres que los apartan de otros miembros de la misma sociedad y que
en conjunto permiten al mercadólogo segmentar el mercado para llegar a las necesidades,
motivaciones, percepciones y actitudes compartidas por el grupo específico. En consecuencia,
todo emprendedor, gerente o investigador, al momento de planificar y ejecutar un estudio de
mercado, debe tomar en consideración esos factores, además de estudiar los siguientes
aspectos:
Costos operativos directos e indirectos y
de instalación del negocio.
Perspectivas de la competencia.
Características del ciclo de vida de los
bienes y/o servicios comercializados.
Evolución de los hábitos del consumidor
meta.
Expectativas de satisfacción de los
clientes actuales y potenciales.
Por otro lado, la globalización impone un régimen de alta competitividad en cualquier
ámbito de la vida moderna, y muy especialmente en el seno de las organizaciones. Entre otros,
la gerencia es variable fundamental para el éxito del negocio, razón por la cual surgen
innumerables técnicas, filosofías o modas gerenciales que se ocupan del servicio y la atención
al cliente. Algunas de las más recientes son la reingeniería de negocio s, la gestión de la calidad
total, la gestión de procesos, la administración total de la mejora continua, el método Tomkins
de mejora continua, los seis sigma, la teoría de las restricciones y el desarrollo organizacional,
entre otros.
Por su carácter totalizador y su desarrollo armonioso, sobresale, sin embargo, la
filosofía japonesa de las 9 s, enfoque cuyo nombre deriva de las iniciales de las palabras
japonesas seiri, seiton, seiso, seiketsu, shitsuke, shikari, shitsukoku, seishoo, seido,
Seiri (ordenar o clasificar)
· Seiton (organizar o limpiar)
· Seiso (limpieza o pulcritud)
· Seiketsu (bienestar personal o equilibrio)
· Shitsuke (disciplina)
· Shikari (constancia)
· Shitsukoku (compromiso)
· Seishoo (coordinación)
· Seido (estandarización).
HERRAMIENTAS LEAN
Estas son las 8 herramientas de Lean:
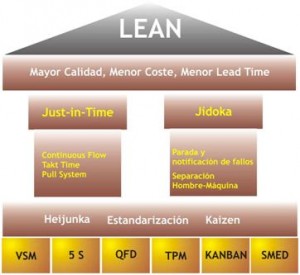
1. VSM (Value Stream Mapping)
Qué es Value Stream? Son todas las actividades en un negocio que son necesarias para diseñar y producir un producto y entregarlo al cliente final.
Qué Es Value Stream Mapping“? Es una herramienta que ayuda a ver y entender el flujo de material e información de cómo se hace un producto a través del Value Stream.
2. 5S es la base de Lean Manufacturing y los fundamentos de un enfoque disciplinado del lugar de trabajo.
5 Pasos para poner al día el lugar de trabajo:
1- Seiri – Clasificar, implica revisar todos los elementos del lugar de trabajo y quitar lo que no sea realmente necesario.
2- Seiton – Organizar, implica poner todos los elementos necesarios en su sitio, definidos, facilitando su localización.
3- Seiso – Limpieza, implica limpiar todo, mantener diariamente todo limpio, utilizar la limpieza para inspeccionar el lugar de trabajo y los equipos para encontrar posibles defectos.
4- Seiketsu – Estandarizar, implica crear controles visuales y pautas para mantener el lugar de trabajo organizado, ordenado y limpio.
5- Shitsuke – Disciplina, Implica mantener una formación y disciplina para asegurar que todos y cada uno sigan las normas de 5 S.
Beneficios de 5S
- Seguridad
- Eficiencia
- Calidad
- Eliminar desperdicios
- Control en lugar de trabajo
3. TRABAJO ESTANDARIZADO, sincronización entre el Tiempo Ciclo y el Tiempo Takt
Hoja de Trabajo Estandarizado
- Proporciona instrucciones claras y completas para el operador.
- Organiza métodos de trabajo sin exceso de desperdicio.
Takt Time, Es el tiempo requerido para hacer una pieza de acuerdo a la demanda del cliente.
Tiempo Ciclo
Tiempo mínimo requerido para realizar un ciclo de una secuencia de trabajo.
- Tiempo de trabajo manual: es el tiempo que toma al operador para realizar un proceso.
- Tiempo maquina: es el tiempo en el que la maquina realiza una pieza
8 Tipos de Desperdicio
1. Sobreproducción.
2. Retrabajo
3. Transporte
4. Defectos
5. Inventario
6. Espera
7. Movimiento
8. Ideas no utilizadas
4. MANTENIMIENTO PRODUCTIVO TOTAL (TPM)
TPM es una metodología que asegura mejoras rápidas y continuas en la manufactura al eliminar averías en los equipos
Esta metodología la basamos en actividades de:
- Mantenimiento Predictivo
- Mantenimiento Preventivo
- Mantenimiento Correctivo
5. ERROR PROOFING
Error Proofing es un proceso de mejora para prevenir un defecto específico que pueda ocurrir.
6. SET UP REDUCTION
Un método para analizar y reducir significativamente el tiempo de cambio de modelo.
Cambio de Modelo
El tiempo entre la última pieza de una corrida de producción y la primera pieza de la siguiente corrida de producción después del cambio.
Internas
Actividades desempeñadas mientras la máquina esta parada.
Externas
Actividades realizadas mientras la máquina esta produciendo
7. FLUJO CONTINUO
Es un sistema de manufactura en el cual los procesos de producción de adelante jalan a los de atrás.
Un sistema efectivo será:
- Producir lo que el cliente demanda
- Proporciona un control visual de un sistema de producción Material (Cantidad, tipo, localización )
- Fácil de observar si la producción esta adelantada o atrasada
- Si los procesos de producción están trabajando al mismo paso, tiene un programa de producción que se regula por si mismo
- Elimina la re-evaluación continua de las necesidades de producción y resultara en incremento real en la productividad por la producción solo de productos costeables
(Kanban)
- Estandarizar Inventarios en Proceso
- Controlar la producción y el manejo del material
- Herramienta de control visual, para administrar estaciones de trabajo
- Elimina la sobreproducción
- Estandariza los procesos de producción
- Minimiza la cantidad de producto en proceso
- Identifica cuellos de botella en el proceso
6 Reglas de Un Kanban
1.- Los últimos procesos siempre tiran de procesos a anteriores
2.- Produce solo la cantidad tomada del proceso anterior
3.- No hay producción o comunicación si no es hecha por una tarjeta kanban
4.- Kanban debe estar adjunto a las partes actuales
5.- Defectos nunca son mandados al siguiente proceso
6.- Revisión periódica del numero de kanban emitido
TIPOS DE DESPERDICIOS
Los tipos de desperdicios
Desperdicios
La Escuela Toyota reconoce siete tipos o categorías de desperdicios:
Desperdicios de la sobreproducción Es el desperdicio por excelencia, y obliga al productor a efectuar correcciones y mejoras.
Desperdicios de la espera Corresponde a los tiempos muertos en una cadena o al trabajador pendiente de una máquina automática.
Desperdicios del transporte Cuando una parte se moviliza a distancia en forma innecesaria, se almacena y se vuelve a utilizar.
Desperdicios del proceso mismo Es derivado de un pobre desempeño de los factores causales y que traslada esta característica al ítem o parte correspondiente.
Desperdicios por almacenamiento innecesario Ocurre por stocks innecesarios derivados de un sistema de producción inapropiado.
Desperdicios por movimientos innecesarios Un deficiente diseño ergonómico obliga a movimientos innecesarios de los trabajadores.
Desperdicios por productos defectuosos Corresponden a desperdicios de los factores causales, así como de tiempo y dinero.